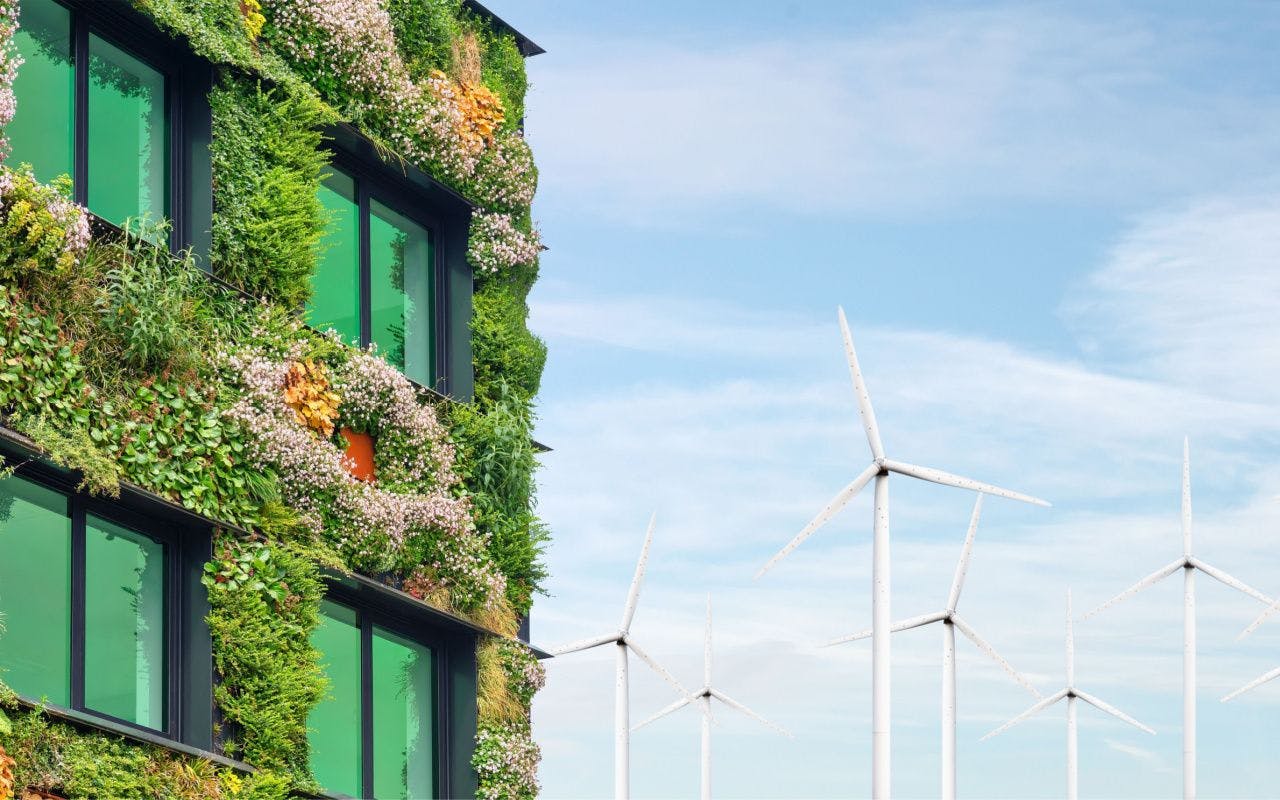
Sustainability Made Simple: How Construction Can Build Better
Construction stakeholders know that the industry—accounting for 11% of global energy-related carbon dioxide emissions—needs to take steps to improve sustainability. An SAP survey showed that most organizations that set sustainability goals fall short of achieving them. But that same surveyed revealed that 47% of engineering and construction executives said that sustainability is a major concern.
How can those industry leaders approach bids and RFPs in a way that signals their commitment to sustainability but also acknowledges the realities of cost, supply-chain, skilled-labor and other issues?
One approach considers a holistic framework that presents stakeholders with all the ways sustainable practices might be applied to their project, and the pros and cons of each. Those stakeholders can then choose which practices are most appropriate and cost-effective for a specific project. One such initiative, like the Living Building Challenge from the International Living Future Institute, prescribes a comprehensive approach to sustainability in the creation of workspaces and buildings.
The LBC challenges companies to build structures and spaces that are not just climate neutral but regenerative, meaning that they have a net positive impact on the environment and their communities. The standards of the LBC are divided into seven performance areas, or petals:
Place
Water
Energy
Health & Happiness
Materials
Equity
Beauty
The guidelines are intended to be applied to all aspects of a new structure or build-out, and they are rigorous, so much so that there are only 24 projects in the world currently pursuing LBC interior accreditation. But all these petals can be represented in the construction phase, which makes them useful in steering discussions with partners and clients around imbuing specific projects with sustainable techniques and elements.
A recently completed project in Auckland, New Zealand, built in adherence with LBC standards, provides an example of these standards in action. The project, a 6,500 square foot office space, was constructed by Unispace for Arup, a global engineering consultancy. Every aspect of the project was considered for its role in reducing the office’s carbon impact from start to finish, including:
Site selection: Insomuch as contractors and other construction stakeholders are involved in helping to choose a location for a new building or workspace. In LBC projects, preference should be given to a location that promotes sustainable modes of transport and proximity to public transport hubs. For their Auckland workspace, Arup chose a historic building that had been repurposed from a warehouse into contemporary offices. The building is within walking distance of both a commuter rail station and ferry terminal.
Water: During construction, to avoid contaminating local waterways, plasterers and painters were sent to purpose-built facilities offsite to wash their equipment in a sustainable way rather than washing in the sink. Other measures included equipping the office with low-flow faucets and toilets to reduce water use.
Electricity: All the electricity for the project came from renewable sources. The office uses daylight and motion sensors to ensure lights are only used when necessary. To offset embodied emissions and energy waste that could not be avoided during construction, Arup purchased carbon offsets to make the project 100% carbon neutral.
Materials: To support local businesses and minimize CO2 emissions related to transportation, half of the materials used in the Arup project were sourced from New Zealand. All the timber used was Forest Stewardship Council certified, meaning the wood came from responsibly managed forests. The project used recycled and salvaged materials where possible, including the final 130 reclaimed bricks from the basebuild, salvaged sliding doors and acoustic paneling, and the kitchen countertop, which was made from 5,000 pieces of plastic waste. 90% of the materials used in construction were free of toxic ingredients like formaldehyde and chlorobenzenes.
Inclusion, diversity, merit, access and belonging: Unispace partnered with Amotai, the supplier diversity intermediary for New Zealand, to ensure at least 5% of all subcontractors were from Māori or Pasifika background. Also, the workplace is 100% accessible for those of differing abilities. Meanwhile, Arup incorporated elements of Māori heritage and culture into the design of their office as a show of respect for a population that has struggled to maintain their right to hold property and access to natural resources.
Waste: Flooring protection, which is typically discarded after a single-use, was rolled-up and reused on other construction sites. In addition, sawdust and other particulate waste was collected and donated for use in composting toilets. To achieve the highest levels of recycling, offcuts were sorted directly on site. Finally, plastic drums in which electrical cables were delivered to the site were donated to a kindergarten for use as seats and in art projects. All told, 99% of construction waste from the project was diverted away from a landfill.
Construction stakeholders are being compelled to embrace sustainable practices, but that doesn’t mean the issues that have inhibited sustainable construction up to now have just disappeared. Offering buyers and prospective clients a variety of ways to incorporate sustainability into projects will help contractors and others address these obstacles while remaining adaptable and competitive.
Related stories
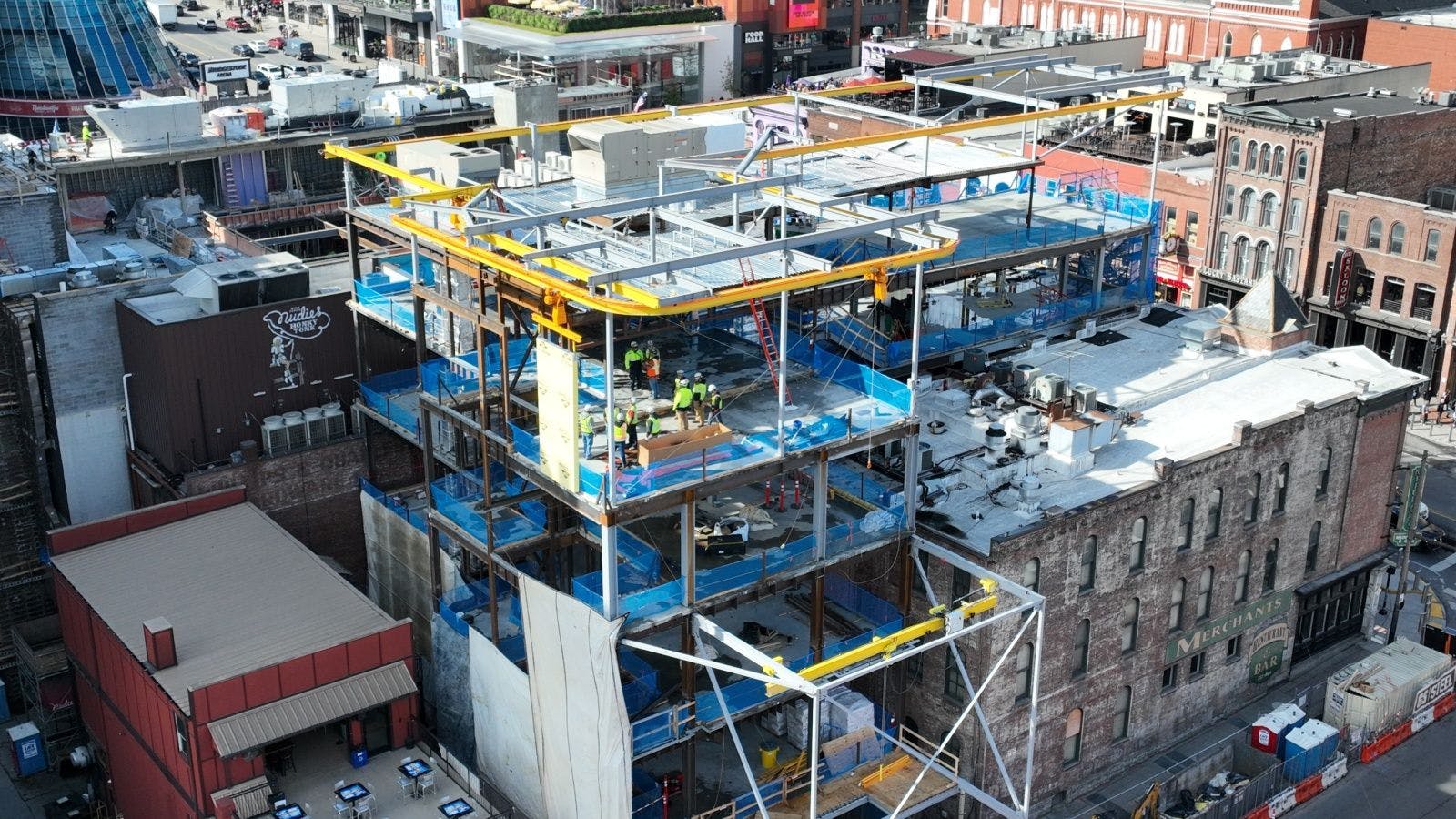
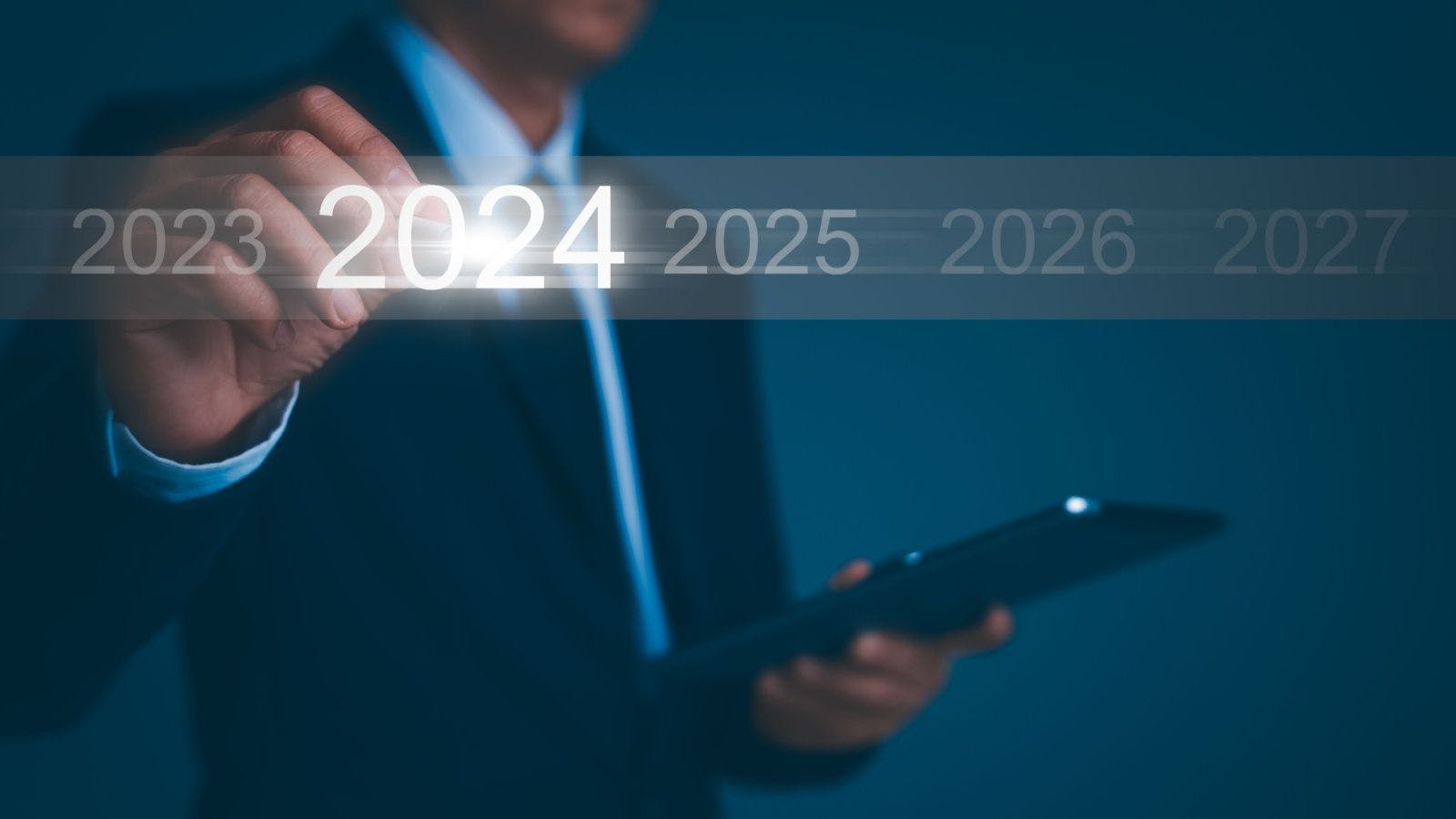
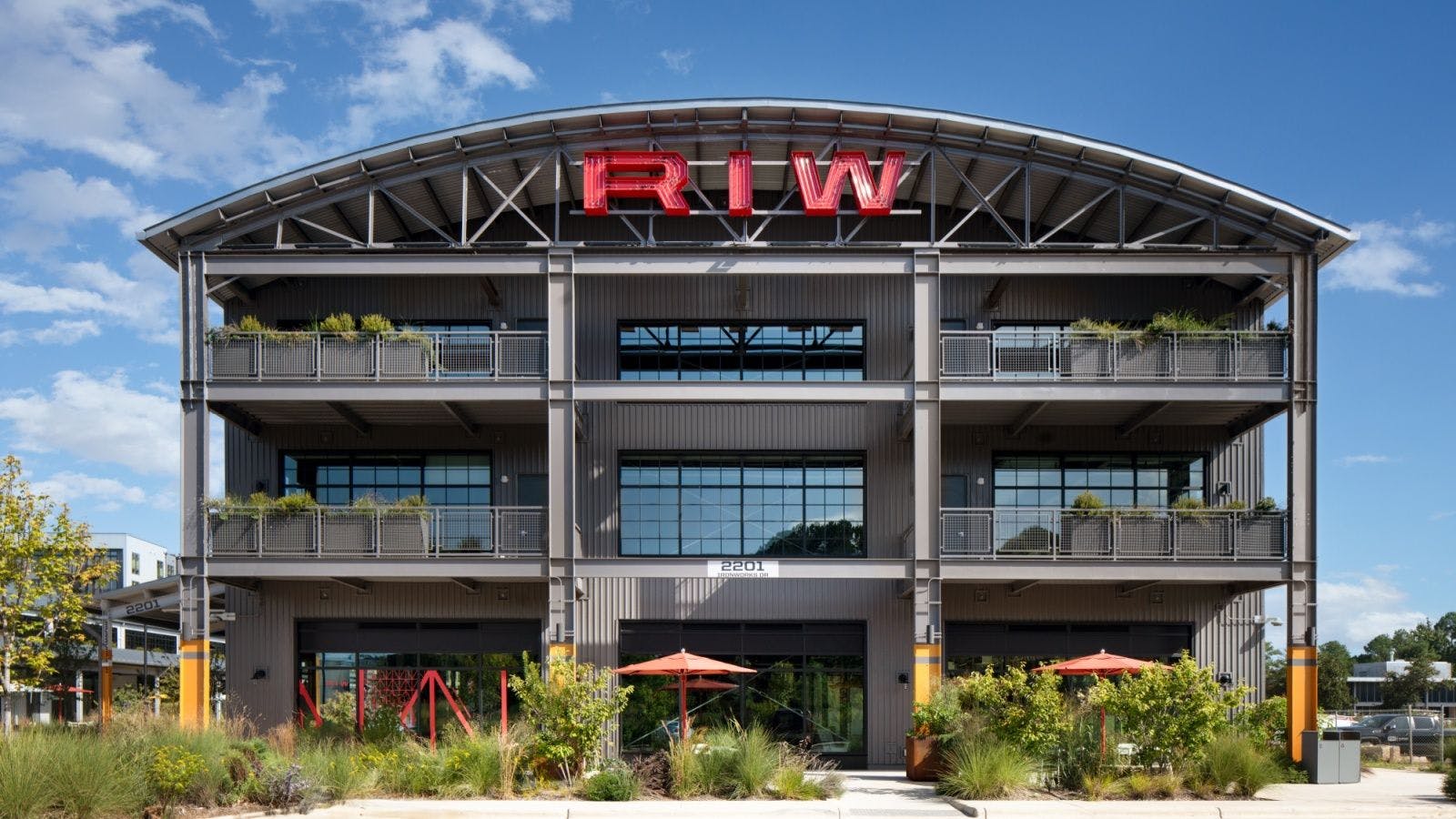