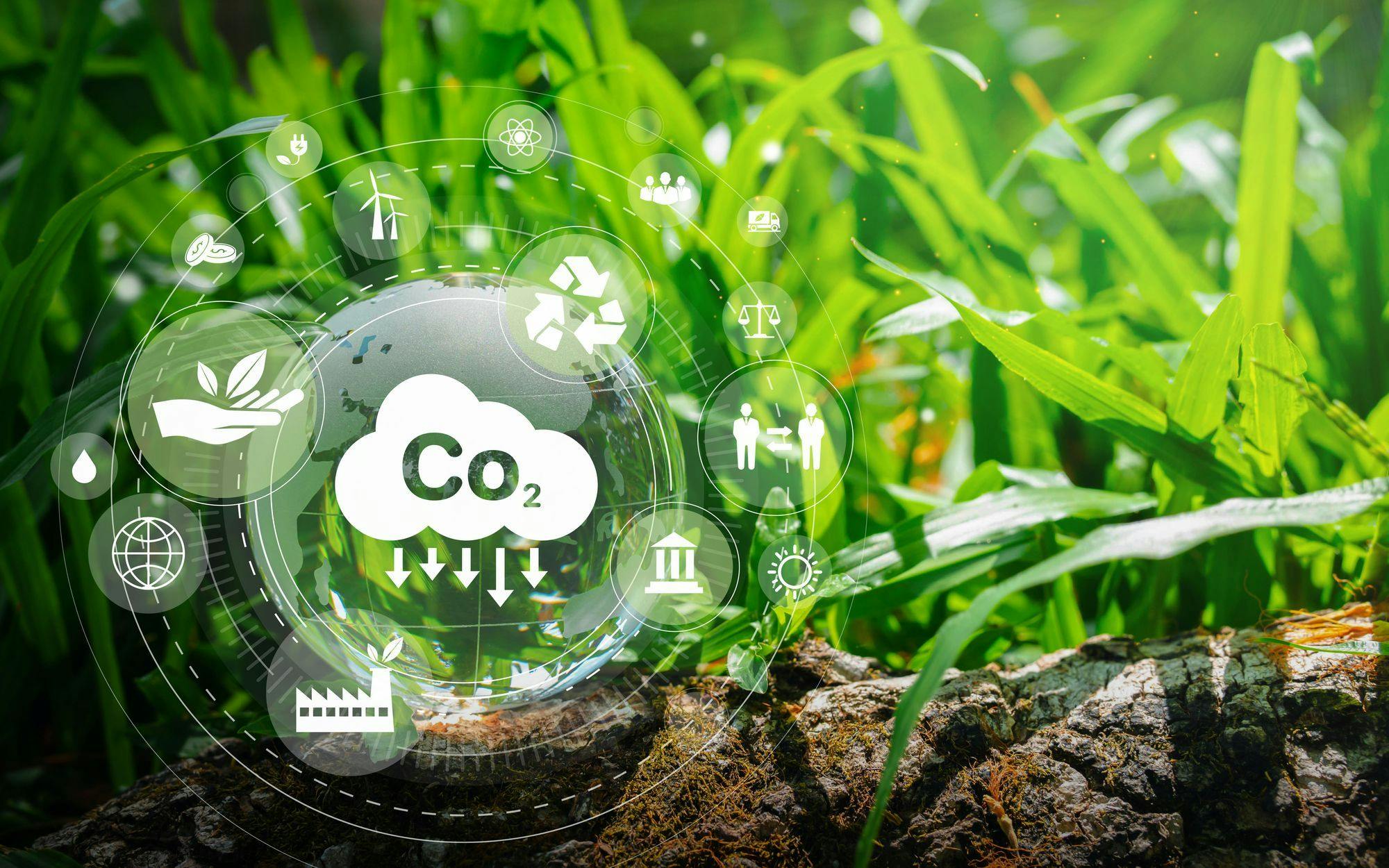
Reduce Greenhouse Gas Emissions With Sustainable Cement
The built environment is expanding and degrading the global ecosystem because traditional construction materials produce surface-level and atmospheric waste. Due to this problem, environmental professionals search for sustainable alternatives to pollution-producing materials.
Cement manufacturing is one of the planet's largest greenhouse-gas-emitting sectors. Currently, scientists and industry professionals are finding sustainable cement alternatives and additives to minimize atmospheric degradation. Reducing cement-related emissions also supports a sustainable concrete industry.
Cement Manufacturing Emissions
Concrete manufacturers rely on cement to support production processes. Cement creates around 8% of global greenhouse gas emissions. The material is ubiquitous and makes up a significant portion of the built environment.
The main ingredient in cement is limestone, which influences its sustainability. Limestone in cement accounts for about half of the material’s direct emissions. Professionals produce limestone by heating calcium carbonate, which breaks down calcium oxide and carbon dioxide. The process accounts for nearly 7% of global emissions.
Manufacturers combine this mineral and clay-like materials in kilns to produce cement, then mix clinker and gypsum to create cement for concrete production. Most kilns run on fossil fuels, which produce greenhouse gas emissions during the combustion phase. A significant amount of construction-related pollution comes from cement kilns.
Greenhouse gas emissions directly pollute the environment as professionals generate limestone for cement manufacturing. Currently, professionals are working on developing sustainable cement advancements to improve environmental conditions.
Low-Carbon, Sustainable Cement Production
Environmental scientists assess each cement material’s impacts to find sustainable solutions. They search for low-emission ingredients to replace unsustainable components. A team of researchers at Stanford University discovered a limestone alternative that reduces greenhouse gas emissions The researchers found that replacing limestone with volcanic rock could significantly improve cement’s sustainability. Volcanic rock produces zero emissions during the production and mixing stages, so they’re now looking for a way to integrate the material into cement production by mimicking hydrothermal environments.
Such environments help volcanic rock mold and recombine without producing pollution. Scientists may recreate elements of the natural system to increase volcanic rock’s compatibility with cementation. Creating new sustainable cement production methods with low-impact materials can help improve global environmental conditions.
Recycle Used Cement
Construction professionals are developing sustainable cement by recycling concrete, minimizing production-related cement emissions over time. Some professionals recycle the building material by pulverizing rubble on construction sites. They use advanced industrial machinery to break up solid materials, then move crushed concrete through a secondary impactor. The device removes contaminants from the rubble and divides large components from smaller aggregates.
Workers can use crushed concrete to build retaining walls, gravel roads and rock gardens. They may also use the material to line streams and banks and minimize erosion. Other individuals reuse larger sections of concrete to reduce waste.
Recycling professionals also discovered ways to recycle cement components directly. They use advanced recycling techniques to turn used concrete into cement waste paste. Using recycled materials in construction significantly reduces energy waste and greenhouse gas emissions.
OffSetting Manufacturing Emissions
Individuals can also create sustainable concrete and cement by offsetting production emissions. Material manufacturers are calculating the carbon footprints of their production processes to improve environmental conservation and use various carbon-offsetting techniques to shrink cement’s carbon footprint.
Cement producers can develop sustainable concrete by investing in renewable-energy projects. Solar and wind farms significantly reduce emissions and help society transition away from fossil fuels. Some producers also install carbon-capturing devices to process and eliminate surface-level pollution at their manufacturing facilities.
Advanced capturing and storage technologies can eliminate emissions by 90% at most. Processing surface-level emissions directly prevents degradation and can help manufacturers develop sustainable cement.
Using Alternative Cement Materials
Manufacturers can also use alternative materials to become more environmentally conscious. They could develop sustainable concrete by sourcing low-impact cement—an essential component of concrete that binds various materials together.
Some researchers are developing concrete from carrot particles. The root vegetable binds materials together and creates a strong aggerate structure; using it in concrete production can increase the material’s strength by 80% on average.
Creating cement with reclaimed plastic also could significantly decrease greenhouse gas emissions and introduce new benefits. Replacing a portion of materials with recycled plastic can create better bend resistance by around 25%. Making further use of plastic water bottles reduces landfill waste and cement production pollution.
Power Kilns with Renewable Energy
Environmental engineers are targeting kiln-related emissions by developing sustainable advancements. One California-based company is using solar and wind energy to power cement kilns.
Using renewables to raise kiln temperatures may shrink cement production’s carbon footprint. Cement manufacturers can use solar and wind power to meet regional net-zero emission goals, helping preserve the atmosphere’s natural conditions. Net-zero emission goals are more achievable than completely eliminating fossil fuels. Individuals can integrate renewables into their production processes to reduce environmental degradation.
Minimizing kiln emissions with renewables also helps manufacturers save money. Wind and solar power are significantly more cost-effective than fossil fuels. Cement and concrete companies can cut costs and improve their financial stability by adopting renewable energy.
Creating Sustainable Concrete
Construction professionals can use sustainable energy sources, additives and cement alternatives to produce low-impact concrete. Concrete comes from cement and is the most extensive building material worldwide. There are few natural spaces left on Earth because the built environment consumes such large quantities of space.
Manufacturers can conserve the natural resources remaining on Earth and preserve lands by developing low-impact concrete. Individuals could use ashcrete to reduce emissions and surface-level pollution. This material comes from nearly 93% recycled materials.
Power plants naturally produce fly ash during the energy production process. Advanced technologies can capture and process fly ash to preserve the atmosphere to minimize cement-related emissions. Replacing a portion of cement with fly ash during concrete production could significantly reduce pollution. Ashcrete generates about 90% fewer greenhouse gas than cement. Reducing ground-level and atmospheric emissions can protect the global ecosystem and human health.
Benefits of Sustainable Cement and Concrete Production
Manufacturers can access economic and environmental benefits when adopting low-impact production techniques. Using alternative materials and energy sources to produce cement can help manufacturing companies save money.
Reducing manufacturing emissions may protect human health, improve ecosystem stability and enhance the conservation of natural resources.
Related stories
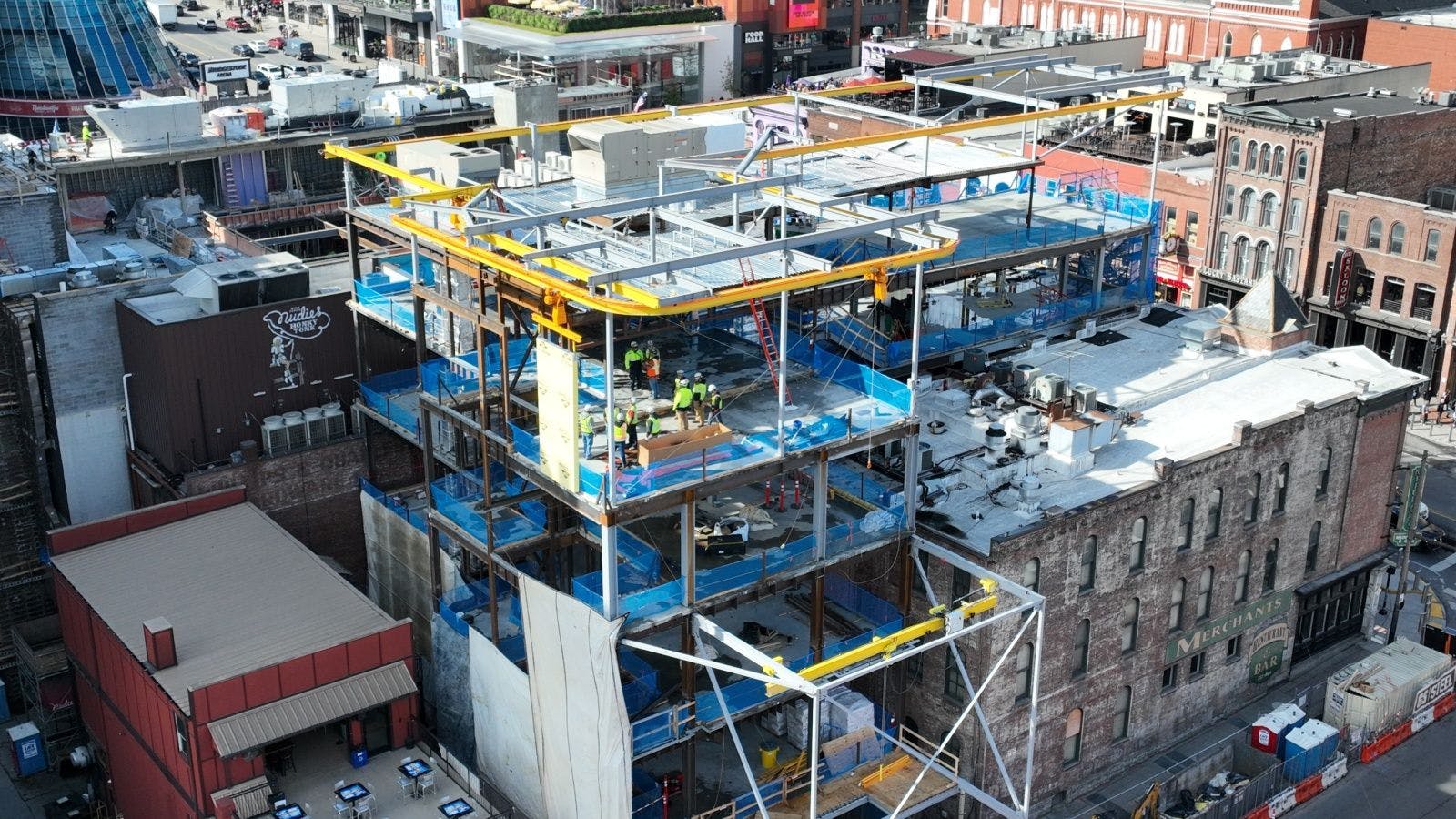
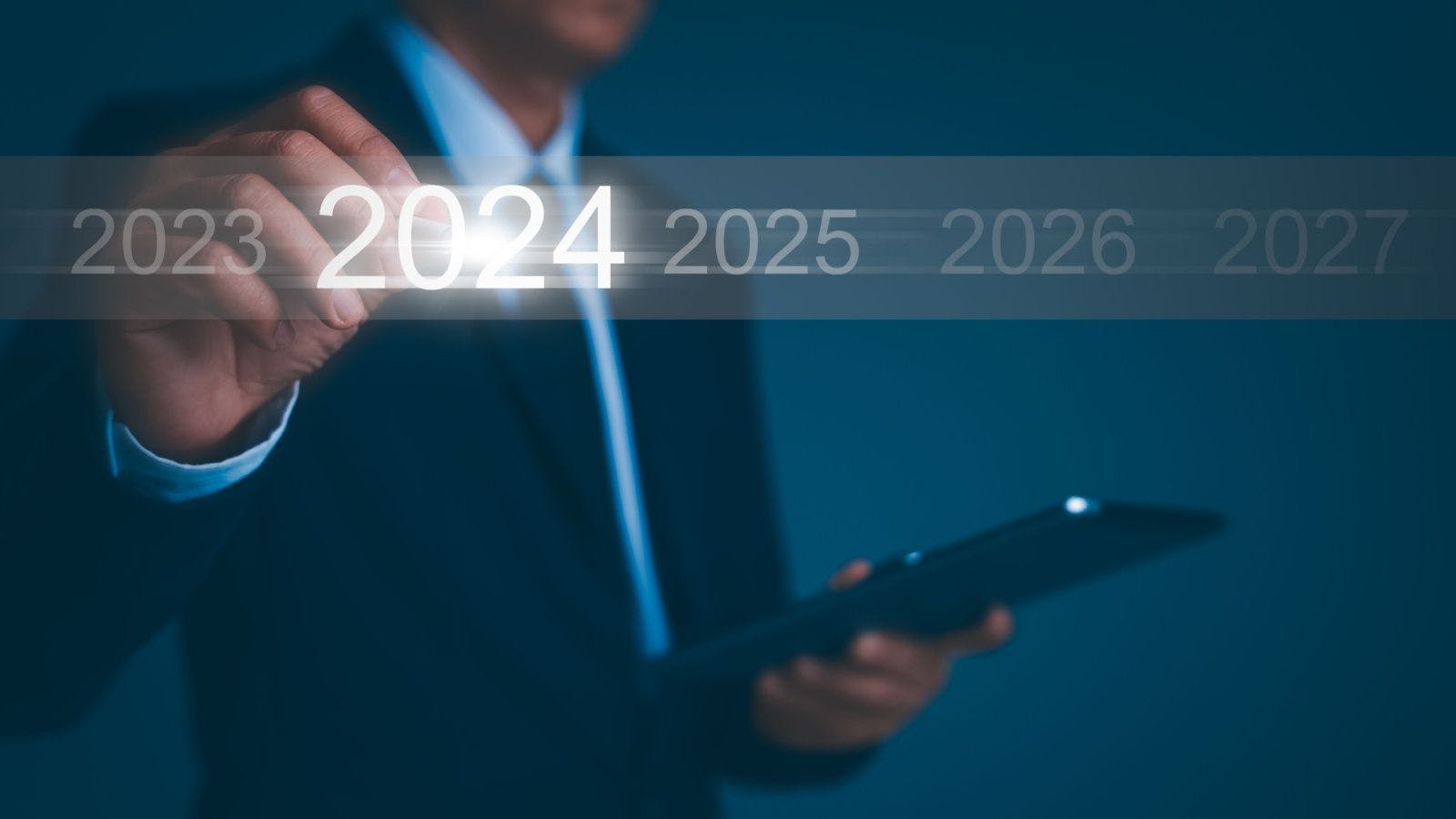
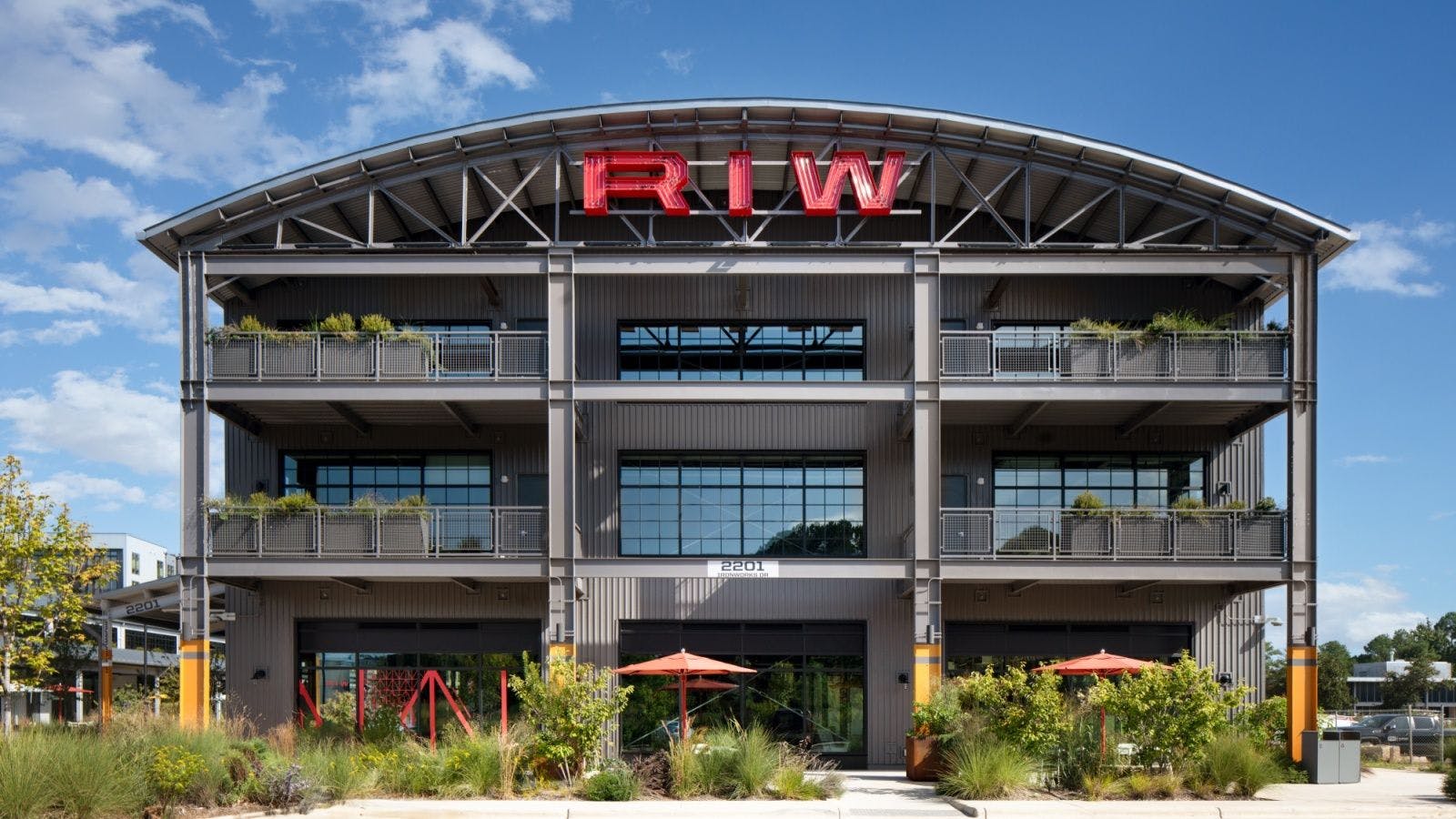