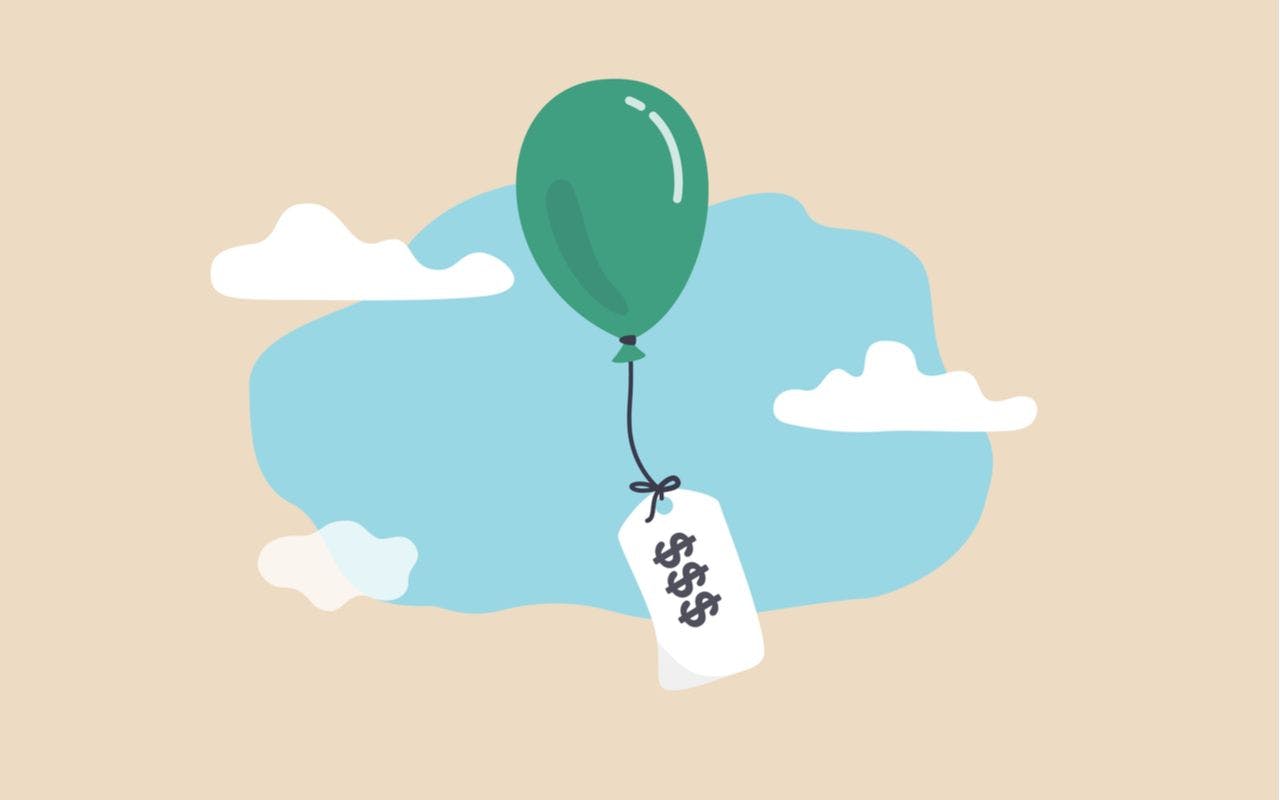
Mitigating the Risks of Materials Price Escalation: Better Now Than Never
The prices of raw building materials have risen dramatically over the past year, primarily because of the global pandemic and trade policies implemented by the previous administration, thereby jeopardizing construction projects that did not mitigate the risks of material price escalation.
Material price escalation is not new to the construction industry, which has experienced historic periods of price escalation known as commodities supercycles, often referred to as periods of time when commodity prices rise above their long-term trends for at least 10 years followed by a downturn of similar duration until supply meets demand. The industrialization of the United States in the late nineteenth century, the post-war reconstruction of Europe and Japan in the 1950s, the oil embargos of the 1970s and the industrialization of emerging nations such as China in the early 2000s are identified as commodities supercycles.
Over the past few months, commodities traders and economists have debated whether a new commodities supercycle is underway as raw material prices continue to rise. The Producer Price Index for July 2021 published by the U.S. Department of Labor, Bureau of Statistics, reported for the 12 months ended in July on an unadjusted basis, that the final demand index increased 7.8%, the largest advance since such data was first calculated in November 2010 and that the final demand index less foods, energy and trade services rose 6.1%, the largest increase since such data was first calculated in August 2014.1
Over the past 12 months ended in July, the price of natural gas is up 146.7%, steel mill products are up 108.6% and crude petroleum and unprocessed energy materials are up 102.9% and 93.8%, respectively. The price of softwood lumber is now up 45.0% after decreasing significantly over the past two months.
While history and the market dictate that prices will eventually come down, it is unclear when or if they will not continue to rise as did the price of copper when it quintupled from 2000 to early 2011. Accordingly, it is in the best interests of all stakeholders - owners, contractors, subcontractors and suppliers - to mitigate risks associated with material price escalation on construction projects.
Several causes have contributed to the rise of raw material prices over the past year and a half. Initially, the production and delivery of many raw materials could not meet demand because of the pandemic due to shutdowns of mills and factories, shipping shutdowns and labor shortages of factory workers, suppliers and transporters becoming ill or having to quarantine or care for others. Supply chain and shipping disruptions have also resulted in delivery delays and long-lead times, driving up prices.
The trade policies of the Trump administration have further contributed to rising raw material prices. In 2017, it imposed duties on Canadian softwood lumber. Then, in early March 2018, it imposed a 25% tariff on imported steel and a 10% tariff on imported aluminum products under Section 232 of the Trade Expansion Act of 1962,2 which resulted in manufacturers raising steel and aluminum prices by those amounts. From 2018 to late 2019, the Trump administration also imposed a 25% tariff on approximately $250 billion of imports from China and a 7.5% percent tariff on approximately $112 billion of imports from China under Section 301 of the Trade Act of 1974.3 In addition to driving up the cost of raw building materials, these tariffs have limited the number of suppliers, which has led to longer delivery times.
Construction stakeholders should consider different strategies for mitigating the risks of price escalations during all phases of a project. During the bidding phase, owners should provide prospective bidders with complete and accurate plans and specifications in order for bidders to estimate the requisite materials for the project. Owners may want to require bids to be submitted pursuant to a cost index such as the ENR Materials Cost Index or AIQS Building Cost Index. On the other hand, contractors, including downstream subcontractors and suppliers, may want to state the time period for which their bids are valid, and include language on their bid forms that any price increases after a date certain are not included in their bids.
These strategies should benefit contractors to the extent they do not have to account for uncertain price volatility in their bids and owners to the extent that they should receive more accurate, competitive bids without built-in contingencies, thereby lowering the overall cost of the project. Owners may also want to allow contingencies or alternates for materials or to break out the project into phases which reduces price volatility because the project is constructed in a shorter timeframe.
Owners can further minimize risk during the procurement phase by requiring that contractors purchase materials subject to volatile pricing soon after the contract is signed, and by providing locations for contractors to store materials delivered to the project ahead of schedule on-site if possible or at an off-site bonded, secure facility. Owners, however, should be reasonably certain that there will not be any design changes to avoid delays and additional costs for materials and transportation.
One of the best ways for stakeholders to mitigate risks associated with material price escalation is to negotiate the form of the contract and method of payment and to include a mutual or bilateral escalation clause. In typical cost-plus and time and materials contracts, owners bear the risk of material price escalations because the contractor is paid for the actual costs of the materials. However, when such contracts include a guaranteed maximum price, the risks of price escalation shift from the owner to the contractor when the GMP is met, unless modified by an escalation clause.
In typical lump sum or fixed price contracts, material price escalation is a bargained for risk negotiated by the parties prior to entering into such contracts. Because of the recent and historic volatility in raw material prices, well-drafted price escalation clauses are essential to construction contracts and to ensuring that projects are delivered with minimum delays and additional costs.
Price escalation clauses may be cost-based or index-based, and generally are categorized as a threshold escalation clause or a delay escalation clause. Such clauses are cost-based to the extent that they compare actual incurred costs to bid costs, and index-based to the extent that they track and provide a mechanism to adjust prices based on an agreed upon material price index such as the PPI or the ENR Materials Cost Index.
A threshold escalation clause allocates the risk of material price increases by obligating the upstream party to pay for such increases above a certain threshold occurring between the dates of the bid or contract price and the purchase of the materials. Under this clause, the risk of price increases lies with the downstream party up to a certain threshold before shifting it to the upstream party, effectively capping the downstream party’s exposure at an agreed upon price.
Alternatively, a delay escalation clause allocates the risk by requiring the downstream party to hold its price for an agreed upon period of time or until a specific milestone before shifting it to the upstream party by requiring that party to provide an equitable adjustment for price increases pursuant to the terms of the escalation clause after that period of time or milestone.
Construction stakeholders should also consider mutual or bilateral escalation clauses to account for not only price escalation, but also de-escalation, of material prices. Such clauses fairly and equitably allocating the risks of volatile price fluctuations often driven by economic and political forces outside the control of either party, allowing upstream and downstream parties to share in the risks and rewards of both material price increases and decreases.
While it is intended to be used with the ConsensusDocs 200, Standard Form of Agreement and General Conditions Between Owner and Contractor (Where the Contract Price is a Lump Sum), the ConsensusDocs 200.1 Amendment No. 1- Potentially Time and Price-Impacted Materials and Schedule A, is a good resource for drafting price escalation clauses.
Under this document, parties identify potentially time and price-impacted materials and establish a method for establishing a baseline price based upon market or catalog prices, actual material costs, material cost indices or some other mutually agreed upon method. This document provides for an agreed upon percentage adjustment to the contract price for increases or decreases in the baseline price, excluding overhead and profit, provided the contractor provides written notice and appropriate documentation substantiating such adjustment. It also provides that the contractor shall be entitled to an equitable extension of contract price and an equitable adjustment of the contract price for the delay in the delivery of, or unavailability of, a potentially time and price-impacted material beyond the control of and without the fault of the contractor or downstream party.
In addition to material price escalation clauses, other contractual provisions may provide a basis for recovery of price increases. A force majeure provision may allow downstream parties to recover for substantial price escalation occurring during the course of the project. To constitute a force majeure event, the contractor or downstream party must demonstrate that the price escalation was an event beyond the control of either party for which the risk was not allocated to one party under the contract that made it impossible or commercially impractical to perform the contract work.
However, even if they clear this high bar, the remedy is not a price increase, but typically only an extension of time excusing non-performance by both parties. A delay damages provision may allow contractors and downstream parties to recover for price escalation or the impact of tariffs if the owner caused delays that prevented those parties from purchasing materials before the escalation or tariff increases. Similarly, a change of law and/or change in tax provision may allow recovery for price increases affected by the imposition of new or increased tariffs and taxes on certain materials.
Careful consideration should be given to mitigating risks of material price escalations during all phases of a project beginning with the design phase and continuing with the bidding, procurement and construction phases.
All stakeholders should collaboratively work to mitigate the risks of price escalations on construction projects by drafting and negotiating contracts that share and transfer such risks fairly and equitably to all the parties. Otherwise, recent and historic material price increases and volatility will lead to adverse, unintended consequences for the parties and construction projects, which is in nobody’s best interests.
Related stories
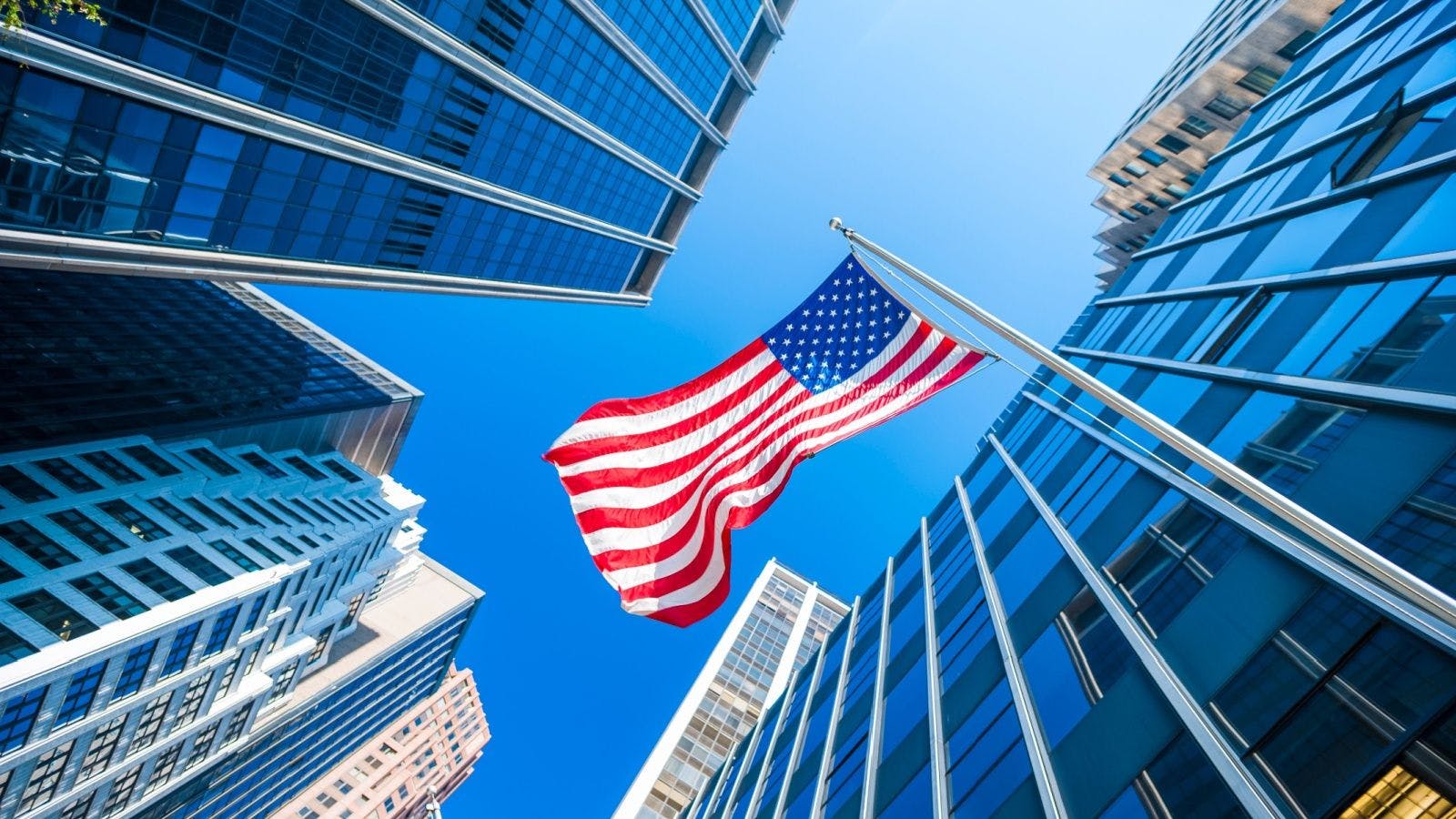
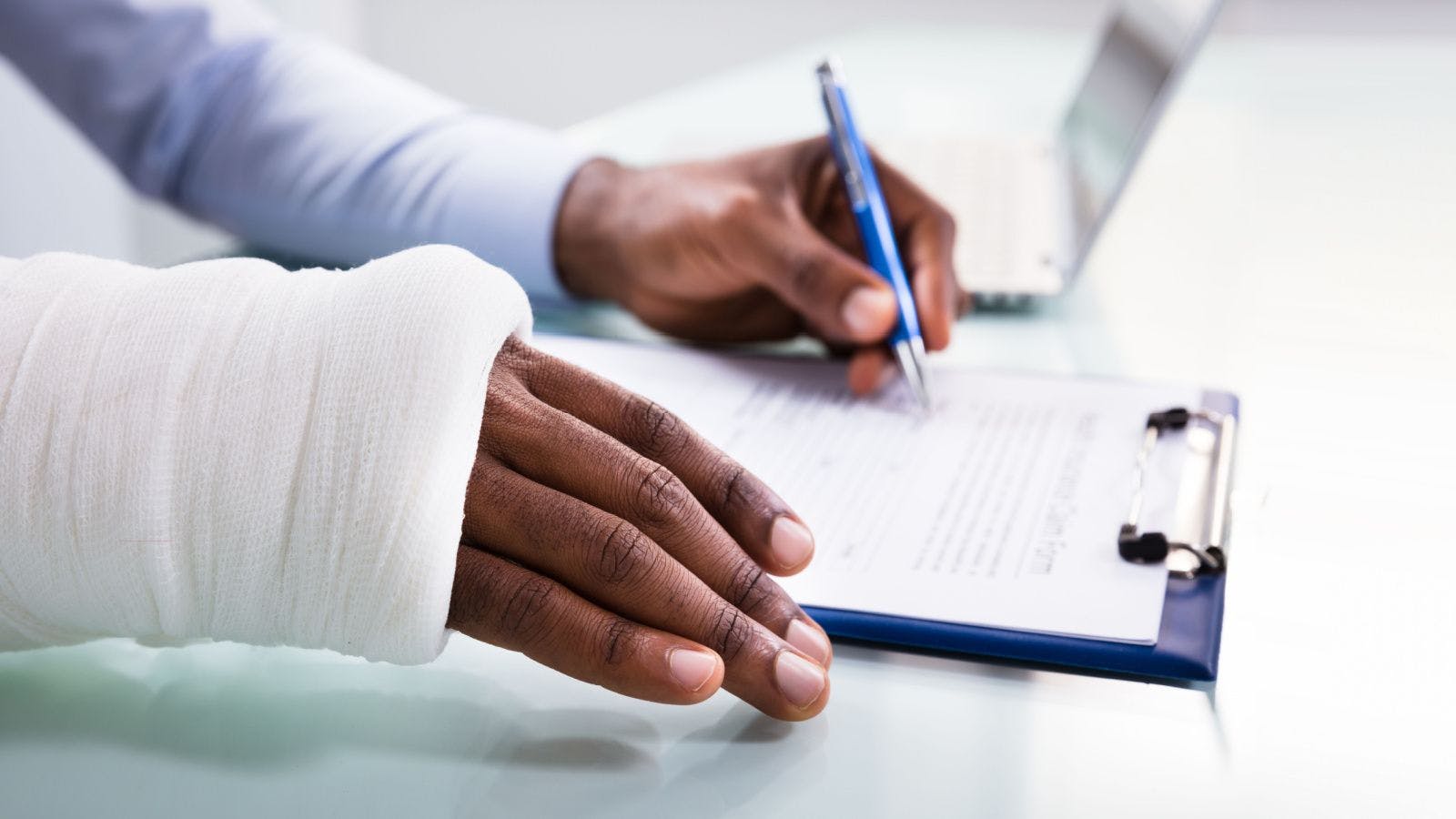
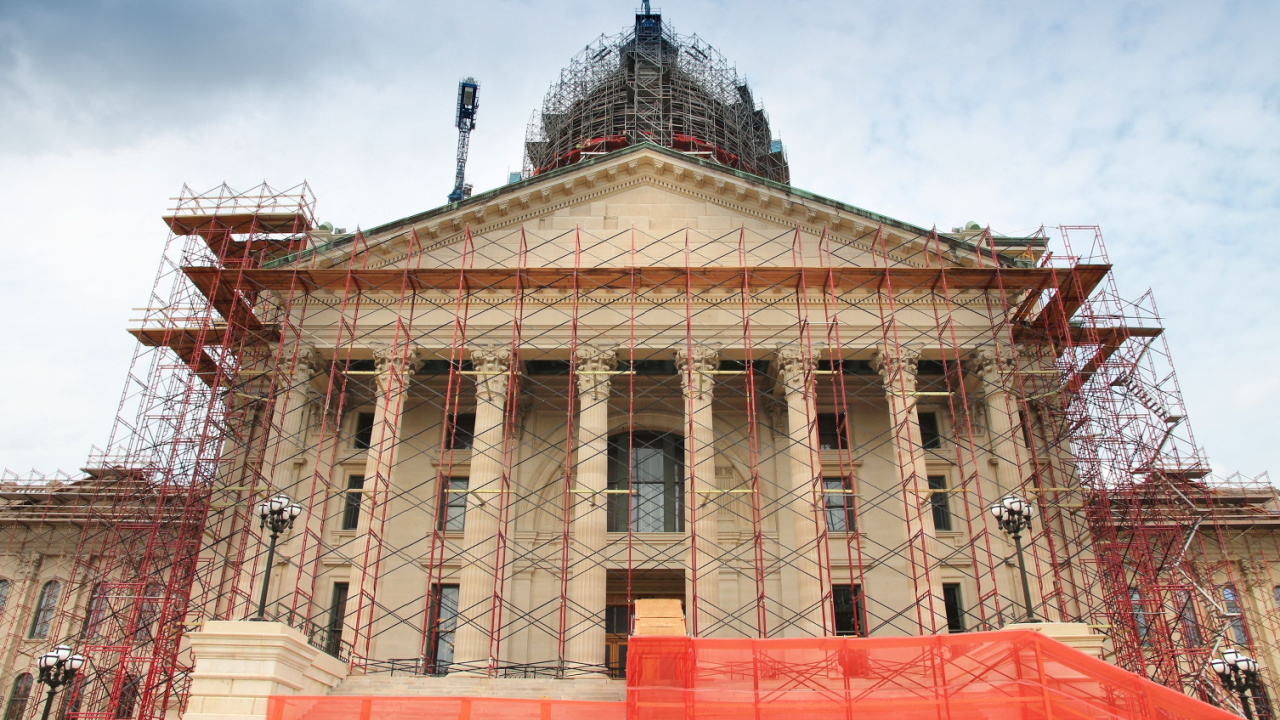