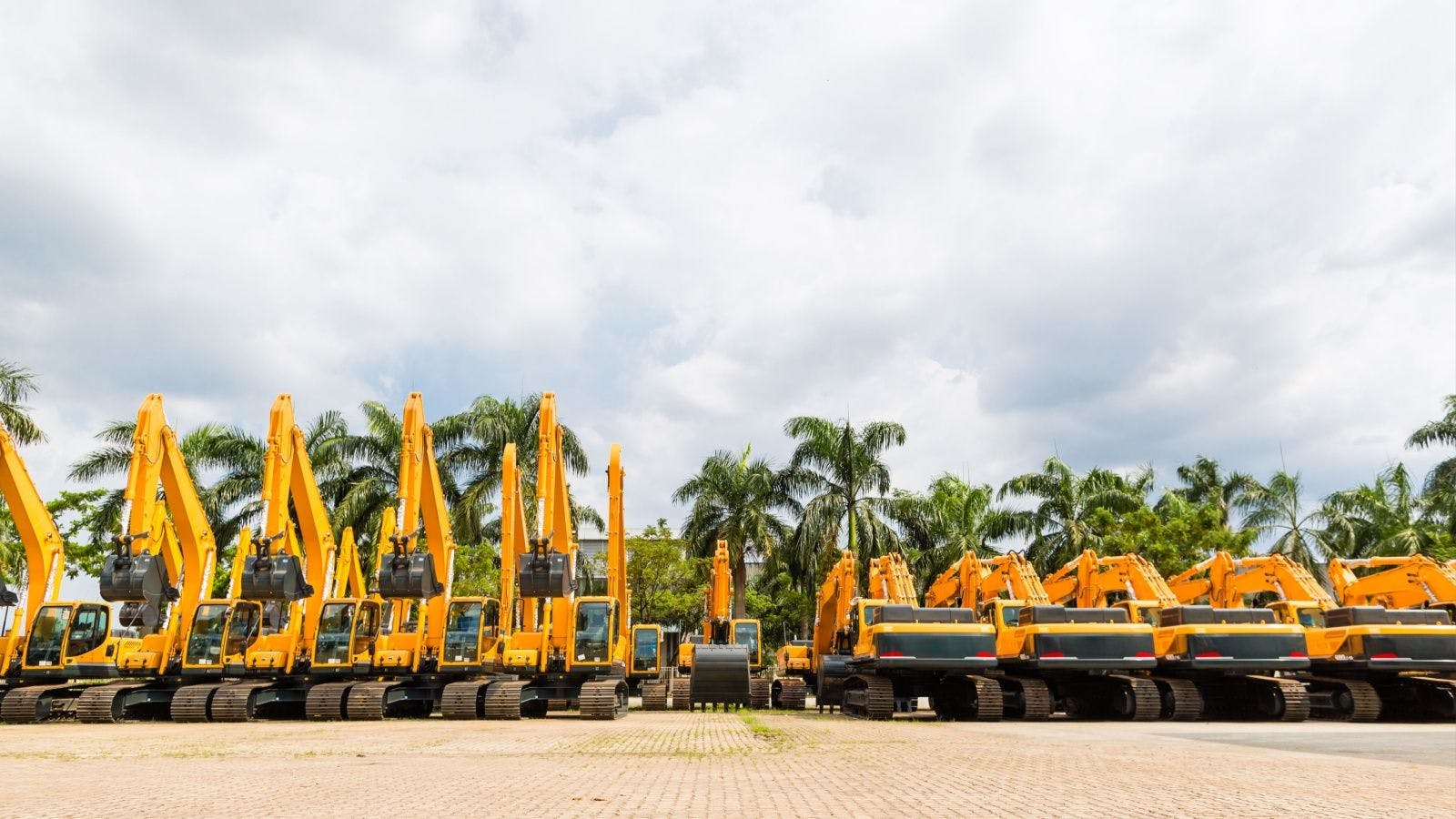
Prioritizing Asset Issues Improves Fleet Productivity
Prioritizing fleet asset issues can significantly improve operational efficiency and productivity, as well as asset performance and return on investment. Construction fleets can implement a structured process for issue prioritization and leverage fleet-management software to proactively address maintenance needs, minimize breakdowns and optimize asset performance.
WHY IT MATTERS
Downed fleet assets aren’t only pricey when it comes to direct repairs, they can also cause costly project delays and additional mechanical and/or equipment damage, as well as safety issues—and all those costs can add up quickly. Even just failure to properly lubricate a cement drum bearing can lead to equipment failure, load loss and, potentially, days of downtime for repairs and chipping the hardened concrete from the drum, if not having to fully replace it.
To mitigate these challenges, fleets can utilize issue prioritization best practices to better manage maintenance tasks based on criticality and urgency. This shift from reactive to proactive maintenance not only minimizes downtime, it also streamlines maintenance workflows for improved productivity.
Issue prioritization requires a structured approach and a clear understanding of priority terms and resolution expectations. By analyzing data, defining priority terms and tracking issue resolution times, construction fleets can optimize their maintenance processes to ensure that critical issues are promptly addressed and crews can complete jobs with minimal delays.
DATA-DRIVEN DECISION MAKING
Fleet data—specifically historical data—plays a major role when it comes to issue prioritization. Having a backlog of historical data can help fleets surface recurring issues among assets to improve preventive maintenance schedules and overall uptime. It can also help inform fleets of service task duration, parts procurement trends (including delays) and types of issues causing downtime versus those that can be safely addressed at a time that doesn’t impact productivity.
To get a full picture of the fleet, as well as detailed asset information, data must be collected from multiple sources, including inspections, work orders, service histories, DTC faults and asset usage. While manually documenting and collecting this data can certainly be done, it can also be time consuming and more prone to error. Automating the data collection processes with FMS enables fleets to easily gain crucial insights into asset health to make informed decisions regarding issue prioritization.
TERMS AND EXPECTATIONS
Clear communication is an essential component in successful issue prioritization. Fleets should establish standardized priority terms and resolution expectations so that everyone on the crew—and in the shop—understands the significance of each priority level. For example, critical issues may require resolution within 24 hours, while high-priority issues may have a resolution timeframe of one to two business days. Being able to apply different severity levels to issues, including critical, high, medium and low priority, helps improve service planning and ensures that critical issues receive immediate attention to minimize downtime and productivity loss.
FMS facilitates issue prioritization by enabling the use of categorization labels in work orders and issues reported from the field, allowing managers to make insightful decisions as issues arise—no matter where the asset is. FMS also provides collaborative features to improve communication fleet-wide, including enabling comments within tasks for easy reference and information consolidation.
TIME TRACKING
Tracking issue resolution duration can help alert fleets to inefficiencies in the service workflow by providing insight into discrepancies between estimated-vs-true time to completion for service tasks. Using this data, fleets can determine the cause of such inefficiencies, including understaffing, parts procurement delays, or simply poor communication around asset issues, and factor unavoidable delays into their issue prioritization strategy.
Construction fleets can utilize FMS to automatically track and monitor service task duration by setting standard duration estimates and comparing those to true task completion times. Technicians can clock in and out of digital work orders to log true hours to completion, as well as add labels to categorize reasons for delay, such as waiting on parts. From here, fleets can gain better understanding of how long services should take on average, enabling better planning for tackling crucial issues expediently.
ISSUE PRIORITIZATION
While prioritizing asset issues is essential for improving fleet productivity, the ability to respond quickly to critical issues requires in-depth insight into fleet operations. Essentially, issue prioritization is still just a cog in a machine of many moving parts; what good is being able to flag and tag issue priorities early without the ability to respond appropriately?
FMS automates the collection, consolidation and aggregation of fleet data—including data from integrated solutions like telematics and other business and fleet software—onto a single platform. This allows data interaction so that the specific key metrics fleets want to view are not only front and center, they’re detailed. Say an asset throws a DTC fault; technicians can look at the associated sensor data to determine if the fault is due to a single component or a system (e.g., dead battery cell versus bad alternator). This level of insight into asset issues better informs what prioritization level should be attached and significantly reduces the time it takes to identify an issue.
Additionally, using data around service duration, asset utilization and status, and asset assignments helps fleets track where and why service delays are happening so they can take steps to improve service workflows and better strategize issue prioritization for reduced downtime and improved productivity.
Related stories
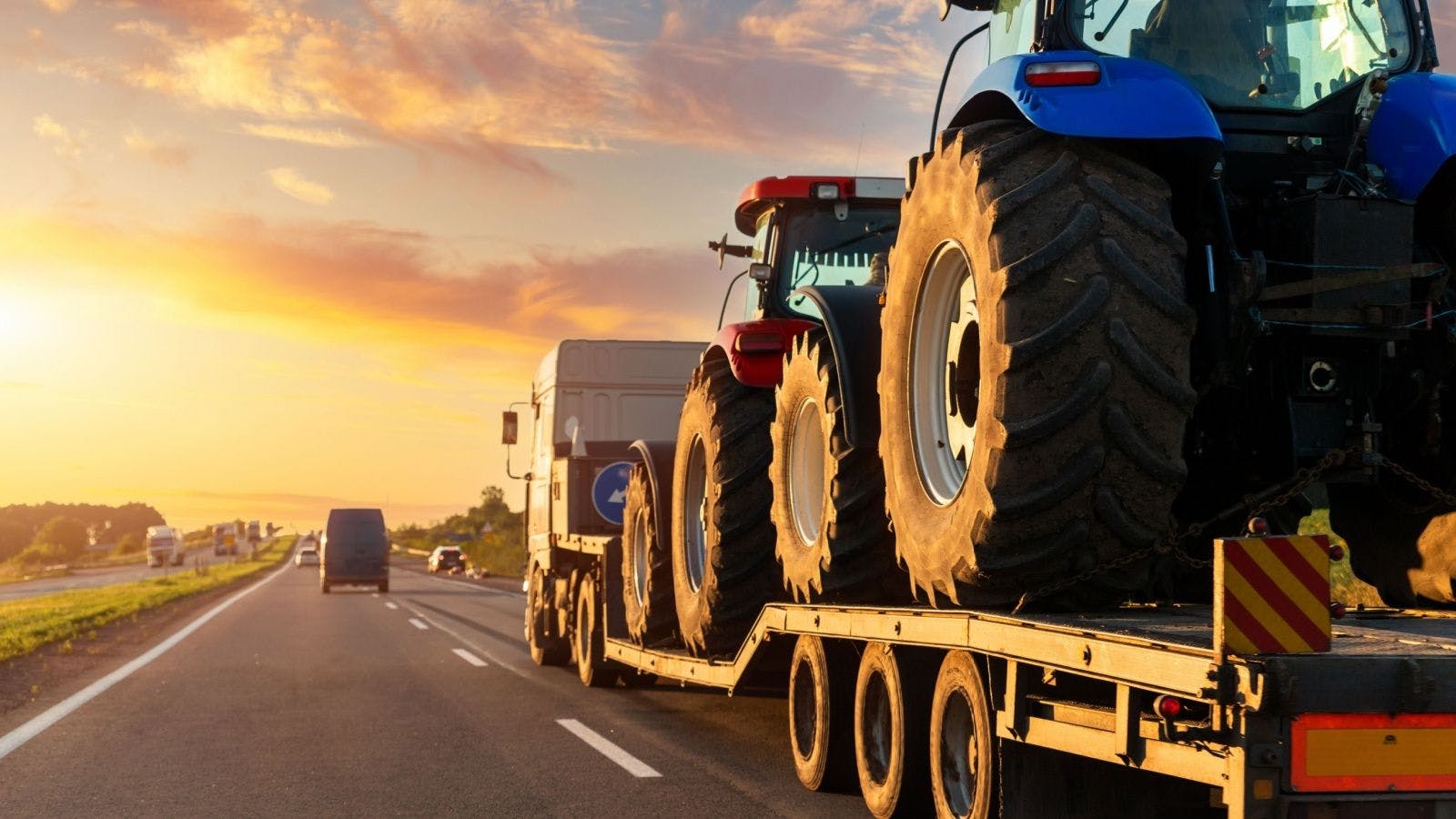
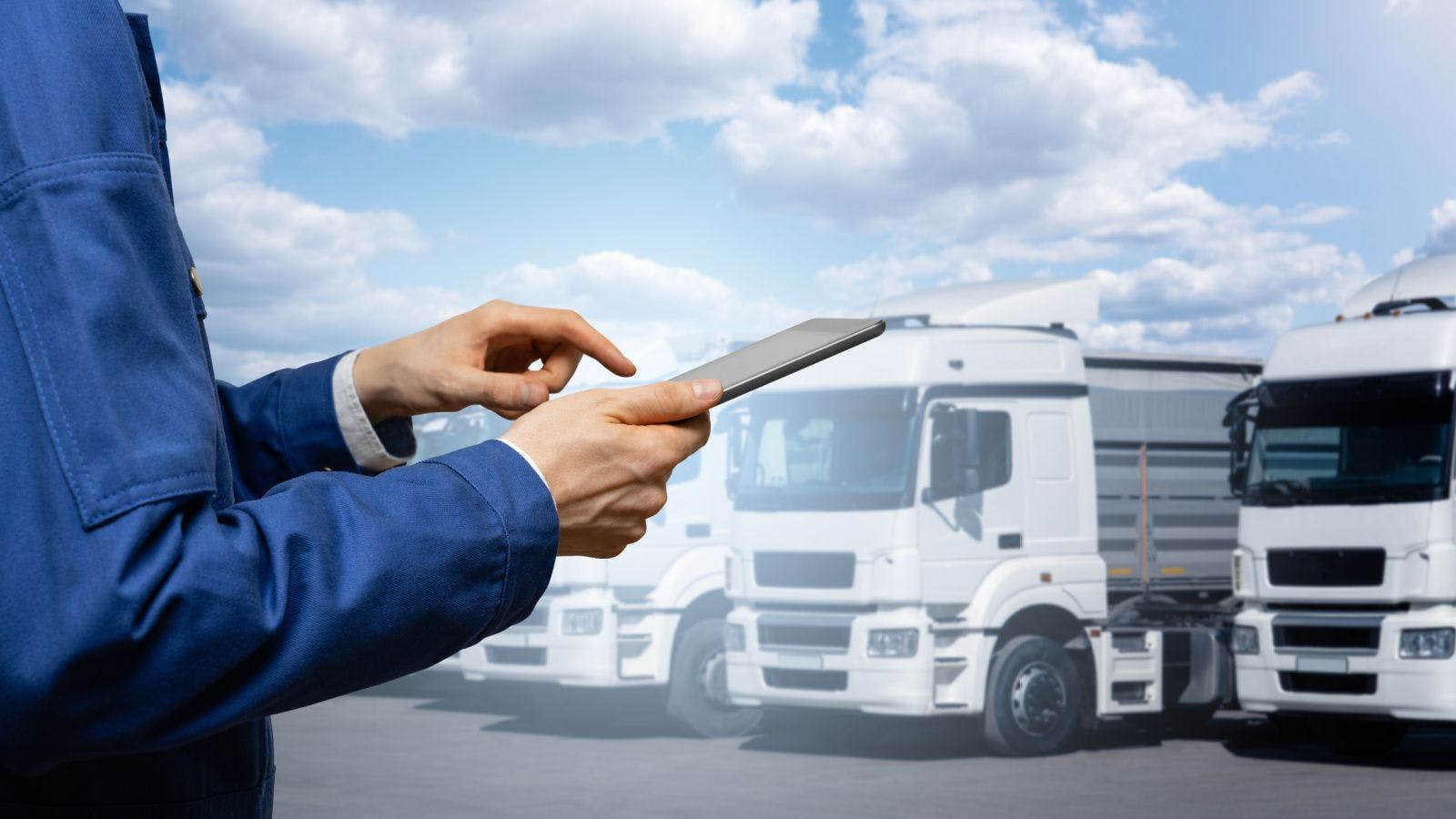
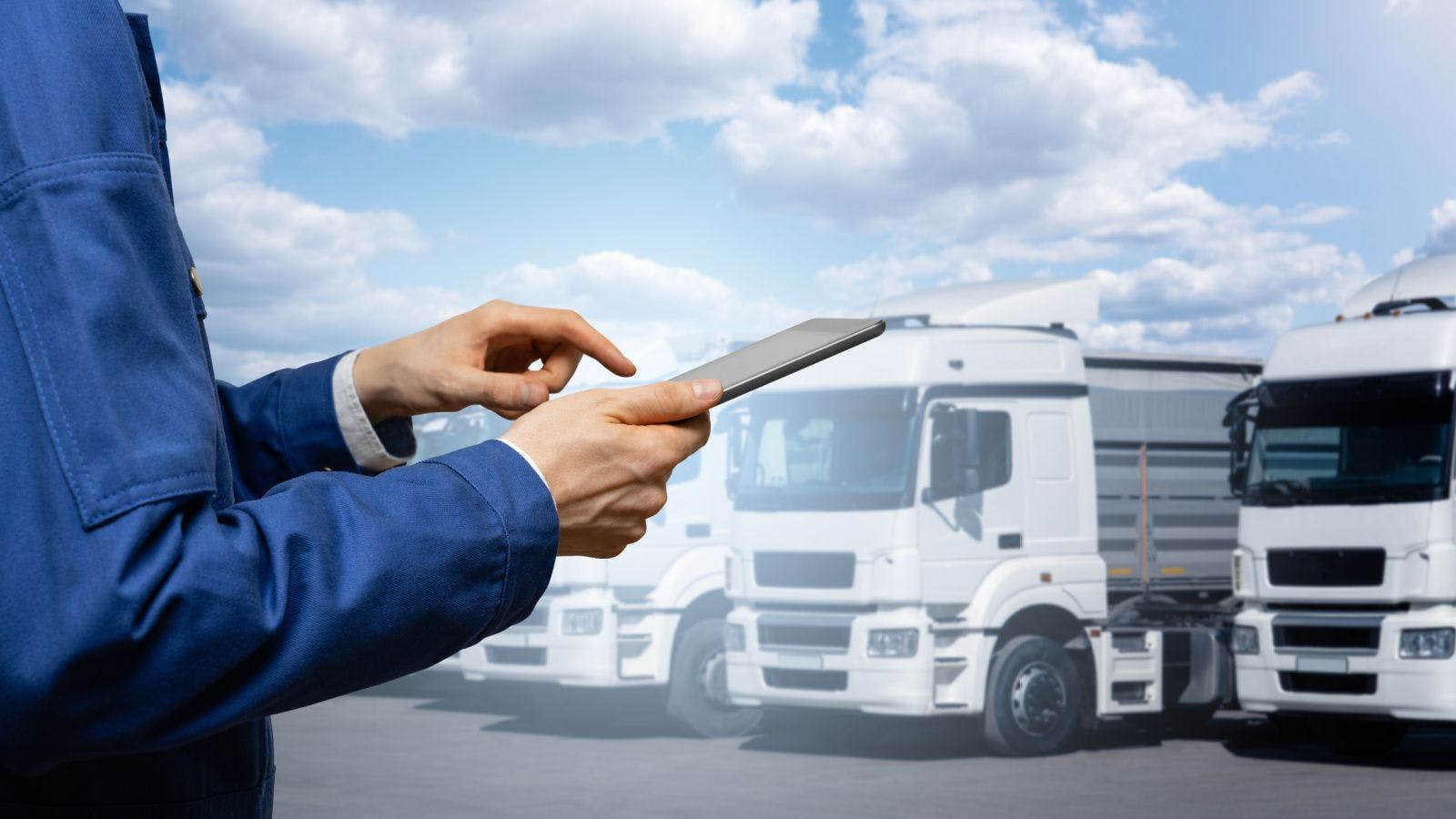